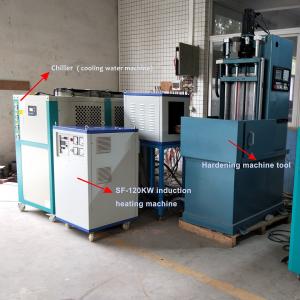
Add to Cart
The principle of gear surface quenching gear quenching principle: the workpiece into the inductor (coil), when the inductor into a certain frequency of alternating current, the surrounding alternating magnetic field is generated. The electromagnetic induction of the alternating magnetic field causes a closed induction current - eddy current - to be generated in the workpiece. The distribution of the induced current in the workpiece cross-section is very uneven, with the current density on the surface of the workpiece being very high and gradually decreasing inwards, a phenomenon known as the skin effect. The electrical energy of the high density current on the surface of the workpiece is transformed into heat energy, which raises the temperature of the surface layer, i.e. surface heating is achieved. The higher the current frequency, the greater the difference in current density between the surface and internal layers of the workpiece, and the thinner the heated layer. The surface quenching is achieved by rapid cooling after the heating layer temperature exceeds the critical point temperature of the steel.
Features:
Induction Quenching Machine is a professional manufacturer of hardening equipment, providing customised vertical and vertical hardening equipment for ball pins, knife edges, pins, automotive shafts, motor shafts, guide rails, rollers, camshafts, crankshafts, etc. The brand name of the machine is Induction hardening machine, with model number DSP-160KW. It is CE, SGS, ROHS and ISO certified and the minimum order quantity is 1. The price is negotiable and the packaging is customised export wooden boxes. The delivery time is 3-15 days and the payment terms are T/T. The supply ability is 100 per month. The control system is PLC Control Box or CNC Control. The quenching precision is ±0.3mm and quenching hardness is HRC50-60. The machine tool colour is customised.
Features | Specification |
---|---|
Easy To Operate | PLC Control Box Or CNC Control |
High Efficiently | Output Frequency: 20-100KHz |
Saving Energy | Heating machine Main components: IGBT |
Induction hardening equipment for large Gears , shaft,, Exporters of hardening equipment Ball pins, knife edges, pins, automotive shafts, motor shafts, Exporters of hardening equipment Ball pins, knife edges, pins, automotive shafts, motor shafts | Input Power: 120KW |
Hardening diameter | 1200mm |
Cooling System | Water Cooling |
Cooling Water Flow Rate | 20L/min |
Product Name | Induction Quenching Machine |
Quenching Precision | ±0.3mm |
Introducing the Induction Hardening Machine DSP-160KW, with CE,SGS,ROHS and ISO certification, offering private customised vertical and horizontal hardening equipment for rails and hubs, exporters of hardening equipment ball pins, knife edges, pins, automotive shafts, motor shafts, etc.
We provide technical support and service for Induction Quenching Machine. We are available 24/7 to help you with setup, maintenance and troubleshooting. We have a team of experienced service technicians who are knowledgeable in all aspects of the machine. We can provide onsite service and repair as well as remote support and advice. We also provide training for operators and maintenance staff on the proper use and maintenance of the machine.
Our technical support and service also includes regular maintenance and inspections to ensure the machine is operating at optimal performance. We can provide spare parts and accessories for the machine as needed. We can also provide custom modifications to the machine to suit your specific requirements. If you have any questions or concerns, our team of service professionals is here to help.
Packaging and Shipping for Induction Quenching Machine
The induction quenching machine is shipped in a heavy-duty wooden crate. The crate is designed to protect the machine from bumps, scratches and other damage during shipping.
The crate is securely fastened with screws and straps to ensure that the machine is safe and secure during transit. The machine is then carefully wrapped in bubble wrap and placed inside the crate. The crate is then labeled with the customer’s address and a tracking number.
The crate is then loaded onto a truck and transported to the customer’s designated address. Upon delivery, the customer must sign for the machine to indicate that the delivery was successful and that they have received the machine in satisfactory condition.