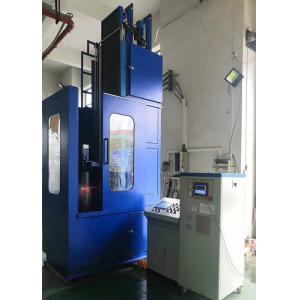
Add to Cart
China Manufacturer Supply CNC High Frequency Hardening Machine tool and Induction Quenching equipment:
Our factory has supplied vertical and horizontal hardening machines to customers in more than 30 countries around the world. We can also provide our customers with customized machines. We have more than 20 years of experience in manufacturing.
The CNC disc&shaft quenching/hardening machine tool is used for CNC induction heating, and the workpiece rotation adopts servo positioning and rotation. The up- and-down movement of the workpiece is driven by a servo motor, driven by a ball screw, guided by a linear guide rail, and a linear bearing. Edit the machine tool's automatic running action and process control action through the CNC program. The bed of the machine tool is welded by section steel structure, which has high strength, good rigidity, and stable and reliable operation. The control system adopts numerical control system, the operation is easy to learn, and the performance is stable and reliable. Rotation control adopts well-known domestic frequency converter, which is stepless adjustable. The general-purpose quenching machine tool for disk and shaft is a new type of general-purpose quenching machine for disk and shaft. It combines the two advantages of large diameter of disk and height of shaft to realize the production of disk products, wheels and ring gears. The overall cooling and quenching of the immersion liquid can also realize the scanning liquid spray quenching process of shafts Model: 2200MM
Technical parameters: (can be customized according to the product)
Maximum quenching length: 2200mm
Work piece vertical running speed: 0-3000mm/min
Maximum work piece diameter: can be customized Control accuracy: 0.1mm
Maximum work piece weight: 500kg CNC system (can be customized according to the product)
The machine tool is composed of bed, control cabinet, quenching load adjustment platform, immersion liquid spray system, overflow system, CNC lifting turntable, cooling water circulation system, transmission system, etc. The work piece rotation, lifting and rotating system is controlled by frequency conversion motor or servo control, and the lifting is driven by servo motor and driven by synchronous belt. The machine tool is easy to operate, and the shaft and disc products are connected to water, which is convenient for use and operation.
1) Induction heating belongs to direct heating of internal heat source, with small heat loss, so the heating speed is fast and the thermal efficiency is high.
2) During the heating process, due to the short heating time, less oxidative decarburization on the surface of the parts, and the scrap rate of parts is extremely low compared with other heat treatments.
3) After induction heating and quenching, the surface hardness of the parts is high, the core maintains good plasticity and toughness, and shows low L] sensitivity, so the impact toughness, fatigue strength and wear resistance are greatly improved.
4) The induction heating equipment is compact, occupies a small area and is easy to use (that is, easy to operate).
5) The production process is clean, no high temperature, and the working conditions are good.
6) Selective heating is possible.
7) The mechanical parts quenched by induction heating surface are small in brittle parts, and at the same time can improve the mechanical properties of the parts (such as yield point, tensile strength, fatigue strength), and the quenching hardness of steel parts that have also been quenched by induction heating surface is also higher than that of ordinary heating furnaces.
8) Induction heating equipment can be placed on the processing line to accurately control the process through electrical parameters.
9) and quenching with induction heating, ordinary carbon structural steel can be used instead of alloy structural steel to make parts without reducing the quality of parts, so under certain conditions, it can replace the chemical heat treatment of process complexity.
10) Induction heating urine is applied to the surface quenching of parts, and can also be used for internal hole quenching of parts, which cannot be achieved by traditional heat treatment.